Companies looking to launch satellites into space typically spend anywhere from $10-50 million per launch but thanks to 3D printing, those costs are set to drop in a big way.
For $4.9 million, businesses can use RocketLab to send small satellites into orbit. The firm's engine, called the Rutherford, is powered by an electric motor and is the first oxygen and hydrocarbon engine to use 3D printing for all its primary components. The New Zealand company is set to begin test flights this year and aims to launch weekly commercial operations next year.
"Our 'Electron' launch vehicle is designed with the purpose of liberating the small satellite market. The whole program is predicated on reducing costs and increasing launch frequency, making space more accessible to everyone" CEO Peter Beck told CNBC.
Those two factors are crucial to opening up space travel, widely seen as unaffordable with long wait times to get into orbit, according to Beck. But a 3D printed engine means an engine can be built in just three days, allowing RocketLab to deliver both on cost and frequency.
Read MoreTHIS will becritical for space travel: SpaceX exec
A wide range of companies makes up the small satellite industry, including television services, radio, broadband, and street-mapping. Lower prices are likely to see more small and medium enterprises (SMEs) join the increasingly competitive market. Some 30 companies have already signed up for RocketLab's services, ranging from governments to universities, Beck said. He counts Khosla Ventures and Lockheed Martin as among his key investors.
"Over the past couple of years, we've seen a tremendous amount of private capital go into small satellites, we're witnessing the democratization of space. Space was really the domain of governments, and now it's moving into private commercial world," Beck said.
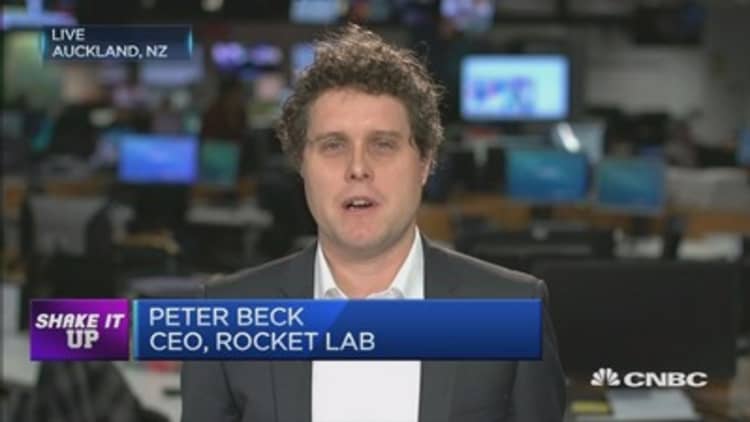
The size and cost revolution
Rocketlab is one of many firms turning to 3D printing to transform the space industry. NASA recently joined the cost revolution by 3D printing the first full-scale, copper rocket engine part.
"Our goal is to build rocket engine parts up to 10 times faster and reduce cost by more than 50 percent," said Chris Protz, a NASA propulsion engineer in a statement. "We are developing a repeatable process that industry can adopt to manufacture engine parts with advanced designs. The ultimate goal is to make building rocket engines more affordable for everyone."
Copper is an ideal material for lining an engine combustion chamber, where temperatures can reach extremes, since it conducts heat better than most metals, NASA explained.
Meanwhile, last July saw SpaceX launch a rocket with a 3D-printed valve body in one of its engines.
"Compared with a traditionally cast part, a printed valve body has superior strength, ductility, and fracture resistance, with a lower variability in materials properties. The valve body was printed in less than two days, compared with a typical castings cycle measured in months," the firm said in a release last year.
The American aerospace firm, founded by billionaire entrepreneur Elon Musk, has already created a printed engine chamber that took only three months to make.
"This will ultimately make the spacecraft fully and rapidly reusable - able to be refueled and reflown multiple times, drastically lowering the cost of space travel," SpaceX said.